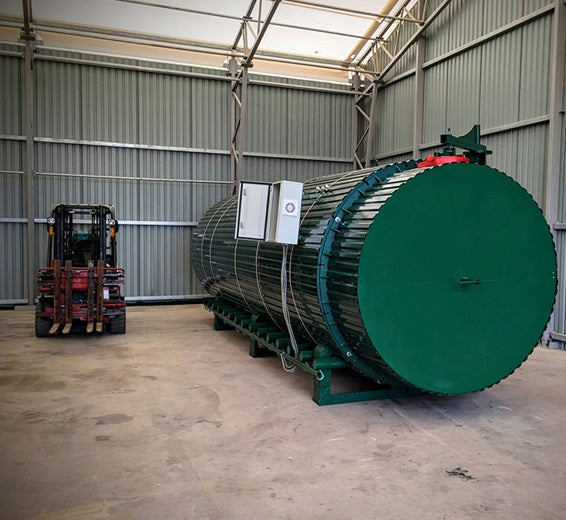
THERMAL MODIFICATION
The thermomodification manufacturing process is based on the use of high temperature and steam. No chemicals or additives are used in the heat treatment process. This process improves the dimensional stability and biological resistance of the wood. It also improves the thermal insulation properties of the wood, as the thermal modification process reduces thermal conductivity. Thermal treatment removes resins from wood.
When wood is heated, some of its chemical and physical properties change. The changes in properties are mainly due to the thermal destruction of hemicellulose. The desired changes begin to appear already at a temperature of 150ºC and do not stop as the temperature gradually increases. As a result, the level of swelling and shrinkage is reduced, the durability is improved, the color is darkened, some extractive substances are released, the equilibrium moisture level is reduced, the acidity "pH" is reduced, and the thermal insulation properties are improved. However, the strength and hardness of the wood also changes.
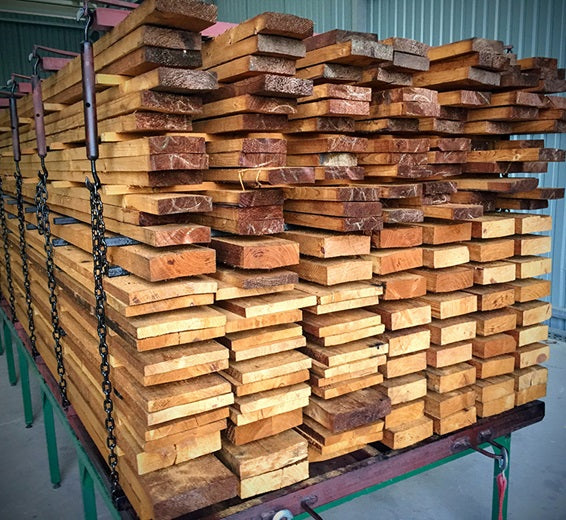
Stages of the heat treatment process
Steaming of wood
At this stage, the temperature in the chamber rises to 130 degrees Celsius, there is water in the chamber, and at a temperature of about 100 degrees, the water in the chamber and the wood begin to evaporate, so the wood is steam dried. , steam is a natural protection against wood splitting. The steam also softens the wood, preparing it for chemical changes and modification.
Thermal modification
The temperature level in the chamber rises to 185-225 degrees Celsius. The maximum temperature depends on the desired end result depending on the application. After reaching the maximum temperature, it is fixed for 2-3 hours (the time depends on both the type of wood and its quantity and geometric dimensions). The steam environment protects the wood from fire and also affects the chemical processes in the wood.
Cooling
The temperature level in the chamber is reduced to 50-60 degrees Celsius, after which the wood is ready for further processing.
Thermo wood properties
Density
Density is measured by comparing the weight and dimensions of the sample. The unit of measurement is kg / m3. The thermal modification process reduces the density by an average of 10%.
Strength
In general, the strength of wood is directly related to the density. Due to the decrease in density during heat treatment, the strength also decreases, but the ratio of weight and strength practically does not change.
Flexural strength and modulus of elasticity
Material treated at temperatures below 200 degrees Celsius is not subject to significant flexural strength loss. A significant decrease in horizontal bending strength is observed in materials treated at temperatures higher than 200 degrees Celsius. Material treated at these temperatures is not recommended for horizontal loading, but only for structural use (vertical load or thermal insulation).
Compression force
The compressive strength depends on the actual density of the wood. According to the test data, heat treatment of wood does not significantly affect the ultimate compressive strength.
Resistance to decay
Thermally treated wood is less resistant to decay. The higher the heat treatment temperature, the lower the resistance to cracking. On average, resistance to decay decreases by 30-40%.
Bolt storage option
This ability is directly related to the density of the wood, pre-drilling a hole with a smaller diameter gives better results.
Hardness
The increase in performance is negligible and has limited effect on hardness.
Moisture balance
Heat treatment reduces the equilibrium moisture content of the wood. When exposed to the highest temperatures, moisture can be 40-50% lower compared to untreated wood.
Swelling and shrinking due to moisture
Heat treatment significantly reduces radial swelling during tangential delamination. Thermally treated wood is not stressed during drying. The swelling and shrinkage of the wood is very low.
Throughput
The heat treatment process reduces the water absorption of wood by 20-30%.
Thermal conductivity
Tests have shown that thermal conductivity of thermally treated wood is reduced by 20-25% compared to ordinary coniferous wood dried in a conventional oven, which improves the efficiency of the wood's insulating properties.
Fire safety
Thermally treated wood does not fundamentally differ from ordinary wood in terms of fire safety. Fire resistance class - D.
Biological longevity
Standard tests (EN113, ENV 807) performed in the laboratory have shown a significant improvement in biological resistance and biological durability due to the removal of the natural food source from the wood, as well as changes in the chemical and structural composition of the wood.
We recommend not to use heat treatment technology for structures that involve deep contact with the ground and determine the operational characteristics of the entire structure. It is assumed that the corresponding loss of strength is due to moisture and not to micro-organisms.
Real experience shows that the use in structures that ensure deep contact with the soil, but does not have a significant role in the operational characteristics of the entire structure, along with periodic drying of the surfaces, does not cause any significant damage to the material. This is especially true when the soil is effectively drained and the soil itself contains sand and gravel.
Weather resistance
Like most natural materials, this wood is not resistant to UV radiation. As a result, under the influence of direct sunlight, the color changes from the initial brown to gray after a while.
The original color can be preserved with pigment-containing preservatives or preservatives with a UV filter
- When thermally treated wood is exposed to atmospheric effects, the natural humidity during 5 years of operation is twice as low as that of untreated wood.
As with all materials exposed to natural weather conditions, heat-treated wood can develop mold on its surface. Bacteria in the air or dirt from the rain can cause fungus to grow on an untreated surface. However, this is only visible on the surface and can be removed by wiping or scraping.
The most optimal protective coating systems for heat-treated wood were an oil primer and a soluble base alkyd topcoat or a water-based acrylic topcoat.
The thermomodification process can be applied to most types of wood. The process must be optimized separately for each type of wood and taking into account its geometric dimensions.
The smoky smell from thermally treated wood is mainly due to furfural. After a while, the smell disappears and can disappear with the use of a protective surface. VOCs released from thermally treated wood are only fractions of the normal pine components.
No toxic or harmful components were found in thermally treated wood. Such wood has even been tested as a bone substitute. However, if the chips get under the skin, they should be removed as soon as possible, as is done with ordinary wood.
Work with thermally treated wood.